Lith Corporation, founded in 1998 by a group of material science doctor from Tsinghua University, has now become the leading manufacturer of battery lab&production equipment. Lith Corporation have production factories in shenzhen and xiamen of China.This allows for the possibility of providing high quality and low-cost precision machines for lab&production equipment,including: roller press, film coater,mixer, high-temperature furnace, glove box,and complete set of equipment for research of rechargeable battery materials. Simple to operate, low cost and commitment to our customers is our priority.
What is a Prismatic Cell Pack Plant?
A Prismatic Cell Pack Plant refers to a dedicated manufacturing facility where prismatic lithiumion battery cells are assembled into battery modules, and then integrated into complete battery packs. These plants are essential for producing highperformance, highreliability battery systems used in electric vehicles (EVs), energy storage systems (ESS), and various industrial applications such as forklifts, AGVs (autonomous guided vehicles), mining equipment, and marine vehicles.
Unlike cylindrical or pouchtype cells, prismatic cells are rigid, rectangularshaped batteries typically housed in aluminum or steel casings. Their structural stability and modular design make them ideal for integration into battery packs using standardized, scalable processes.
A prismatic cell pack plant may range from a small R&D or pilot production facility to a largescale Gigafactorystyle operation, depending on the production volume and market demand.
What Does a Prismatic Cell Pack Plant Do?
A prismatic cell pack plant performs a full range of operations to convert individual battery cells into fully functional battery packs. These include:
1. Incoming Cell Inspection and Sorting
Cells are tested for voltage, internal resistance, and capacity.
Sorted into performance groups to ensure consistency across modules.
Ensures balanced performance and longevity of the final battery pack.
2. Module Assembly
Cells are stacked and arranged into predefined module configurations.
Includes the installation of:
Insulation materials
Cooling plates
Sensors and brackets
Can be done manually, semiautomatically, or fully automatically depending on the plant’s scale.
3. Busbar Welding
Electrical connections between cells are made using copper or aluminum busbars.
Common techniques:
Laser welding – for high precision and minimal thermal impact
Ultrasonic welding – for thin metals and dissimilar materials
Vision systems and quality control checks are used to ensure weld integrity.
4. Module Housing Installation
Modules are placed into protective trays or housings.
Includes:
Thermal interface material (TIM) dispensing
Fastener installation
Sealing and clamping
Some modules may include integrated liquid cooling channels.
5. Leak and Pressure Testing
For liquidcooled modules, pressure or leak testing is performed.
Techniques include:
Air pressure decay test
Helium leak detection
Ensures no coolant leaks that could damage the battery or affect performance.
6. Module Testing
Each module undergoes:
Voltage and resistance checks
Communication tests with the Battery Management System (BMS)
Functional performance validation
Data is often recorded digitally for traceability and quality assurance.
7. Battery Pack Integration
Multiple modules are mounted into a final battery pack enclosure.
The Battery Management System (BMS) is installed and connected.
Additional components include:
Wiring harnesses
Cooling systems
Safety interlocks
Structural reinforcements
8. Final Battery Pack Testing
Comprehensive testing includes:
Full charge/discharge cycles
Thermal performance checks
Communication and control validation
Ensures compliance with safety and performance standards like UN38.3, IEC 62660, and ISO 26262.
9. Labeling, Packaging, and Dispatch
Each battery pack is labeled with:
Serial number
QR/barcode
Production date and batch information
Packed securely and prepared for shipping to OEMs or endusers.
Types of Prismatic Cell Pack Plants
Depending on production scale, automation level, and application focus, prismatic cell pack plants can be categorized as:
1. R&D or Pilot Plants
Used for prototyping, testing, and smallscale production.
Often semiautomated or manual.
Ideal for startups or companies developing new battery systems.
2. MidScale Production Plants
Designed for moderatevolume output, such as for niche EVs or industrial applications.
Typically include semiautomated lines with some manual handling.
Offer flexibility and costeffectiveness.
3. HighVolume GigafactoryStyle Plants
Largescale, fully automated facilities designed for mass production.
Used by major EV manufacturers or battery suppliers.
Feature:
AI vision systems
Realtime data tracking
MES (Manufacturing Execution System) integration
Highspeed robotic assembly
Battery Mixer
Key Components of a Prismatic Cell Pack Plant
A modern prismatic cell pack plant integrates various advanced technologies and systems:
Cell Sorting and Inspection Stations
Robotic Handling and Assembly Systems
Laser and Ultrasonic Welding Stations
Thermal Management Integration Units
Leak and Pressure Test Chambers
Electrical and Functional Test Benches
Battery Pack Assembly Lines
Final Testing and Quality Assurance Zones
Traceability and MES Integration Systems
Packaging and Logistics Areas
Design Considerations When Building a Prismatic Cell Pack Plant
When planning or setting up a prismatic cell pack plant, the following factors should be considered:
Cell Compatibility: Ensure the plant supports your specific prismatic cell dimensions and chemistry.
Production Volume: Match the layout and equipment to your daily or hourly output targets.
Automation Level: Choose between manual, semiautomatic, or fully automated systems based on budget and scalability needs.
Thermal Management Requirements: Decide whether your design uses aircooling or liquidcooling systems.
Integration with BMS: Ensure compatibility with your Battery Management System for seamless communication.
Safety Features: Include fire suppression systems, emergency stops, and explosionproof enclosures where necessary.
Traceability and Digital Integration: Implement MES and data logging systems for process optimization and quality control.
Factory Layout and Workflow: Optimize the flow of materials and workstations to minimize bottlenecks and maximize efficiency.
Applications of Prismatic Cell Pack Plants
These plants produce battery systems for a wide variety of sectors:
Electric Vehicles (EVs): Passenger cars, buses, trucks, delivery vans
Energy Storage Systems (ESS): Gridscale storage, renewable energy integration, backup power
Industrial Equipment: Electric forklifts, AGVs, mining machines
Transportation: Electric trains, ships, boats, and marine vessels
Benefits of Operating a Prismatic Cell Pack Plant
Enables scalable, repeatable production of highquality battery systems
Offers excellent mechanical stability and thermal management capabilities
Supports both smallbatch and massvolume production
Reduces failure risks compared to pouchtype cells
Facilitates advanced automation and digital monitoring
Improves product consistency and reduces labor costs through automation
Leading Companies Involved in Prismatic Cell Pack Plant Development
Several global companies specialize in providing turnkey solutions or key components for prismatic cell pack plants:
KUKA Systems – Advanced robotic automation for battery assembly
B&R Industrial Automation (ABB) – Integrated automation platforms
Gree EnergyTech – Complete battery module and pack line solutions
Hanson Robotics – Smart battery manufacturing systems
Hyundai WIA – Specialized equipment for automotive battery production
EnerSys – Experts in energy storage system integration
Tesla (inhouse developed systems) – Custombuilt lines for Gigafactories
Need Help Planning Your Prismatic Cell Pack Plant?
If you're looking to design, build, or optimize your prismatic cell pack plant, I can help you with:
Process flow and production planning
Factory layout and space optimization
Equipment selection and automation strategy
Supplier recommendations and cost estimation
Customization based on your specific application and production goals
All you need to do is provide the following information:
Cell dimensions and chemistry
Desired production volume per day
Level of automation needed (manual/semiauto/fullauto)
Target application (EV, ESS, industrial, etc.)
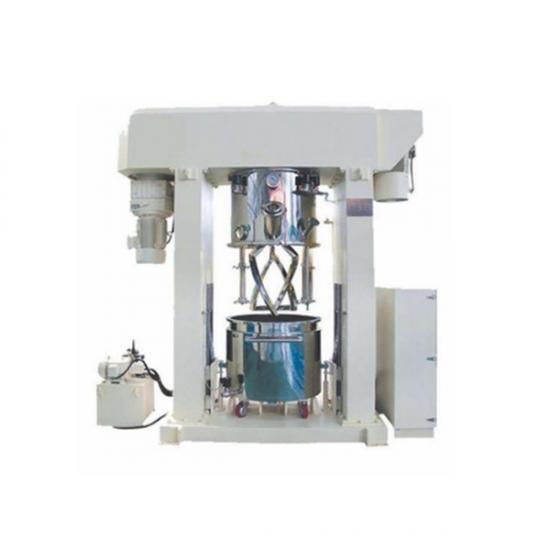