Lith Corporation, founded in 1998 by a group of material science doctor from Tsinghua University, has now become the leading manufacturer of battery lab&production equipment. Lith Corporation have production factories in shenzhen and xiamen of China.This allows for the possibility of providing high quality and low-cost precision machines for lab&production equipment,including: roller press, film coater,mixer, high-temperature furnace, glove box,and complete set of equipment for research of rechargeable battery materials. Simple to operate, low cost and commitment to our customers is our priority.
A Wire Rod Coater is specialized equipment designed to apply coatings onto wire rods, which are long, cylindrical metal pieces typically made of steel or other alloys. This type of machinery is crucial in the manufacturing process for enhancing the performance and longevity of wire rods by applying protective or functional coatings. These coatings can serve various purposes such as corrosion protection, improving electrical conductivity, reducing friction, or adding aesthetic value.
Key Features
1. Coating Application Techniques
Wire rod coaters may use different techniques depending on the desired coating material and application requirements. Common methods include:
Dip Coating: The wire rod is dipped into a bath containing the coating material.
Spray Coating: Coating material is sprayed onto the wire rod using pneumatic or hydraulic spray systems.
Electroplating: A process where an electric current is used to coat the wire rod with a thin layer of metal, such as zinc or nickel.
Powder Coating: Dry powder is applied electrostatically and then cured under heat to form a durable coating.
2. Precision Control
Advanced models offer precise control over the thickness and uniformity of the coating applied, ensuring consistent quality across the entire length of the wire rod.
3. Material Compatibility
Capable of handling various types of wire rods and coating materials, including metals (e.g., zinc, aluminum), polymers, and ceramics.
4. Efficiency and Speed
Designed to operate at high speeds while maintaining precision, making them suitable for largescale production environments.
5. Integrated Drying/Curing Systems
Depending on the coating method, these machines often come equipped with drying or curing systems (such as ovens or UV lamps) to set the coating properly after application.
6. Automation and Monitoring
Modern wire rod coaters feature automation capabilities that allow for realtime monitoring and adjustment of key parameters like speed, temperature, and coating thickness. This helps maintain quality and consistency throughout the production process.
Film Coating Machine
Applications
Construction Industry: Used for reinforcing bars (rebar) and other structural components to enhance corrosion resistance and durability.
Automotive Sector: Applied for wires used in vehicle manufacturing, providing protection against environmental factors and wear.
Electrical Engineering: Essential for wires and cables requiring enhanced electrical conductivity or insulation properties.
Telecommunications: Utilized for coating communication cables to protect against environmental damage and ensure signal integrity.
Considerations When Choosing a Wire Rod Coater
Application Requirements: Assess your specific needs regarding coating thickness, material compatibility, and the type of coating required (protective, functional, decorative).
Production Scale: Select a machine that matches your production volume, whether you need a small unit for custom runs or a highspeed model for industrialscale operations.
Budget Constraints: Balance initial investment costs against longterm operational benefits, considering maintenance, energy consumption, and potential productivity gains.
Ease of Use and Maintenance: Opt for userfriendly interfaces and straightforward maintenance procedures to minimize downtime and training.
Compliance Standards: Ensure the machine meets relevant industry standards and regulations, particularly important in regulated fields like construction and automotive manufacturing.
By carefully evaluating these considerations, you can select a Wire Rod Coater that not only satisfies your current production needs but also supports future growth and compliance requirements. Ensuring highquality, consistent coatings is fundamental to many manufacturing processes, making the selection of appropriate coating equipment a critical decision for manufacturers across various sectors. Manufacturers specializing in this type of equipment often provide a range of wire rod coaters tailored to different applications and scales of production. Consulting directly with these manufacturers can help identify the most suitable model for specific needs. Examples of such manufacturers might include companies known for their expertise in coating solutions, such as SMS group, Danieli Corus, and others renowned for providing robust and reliable wire rod coating machinery.
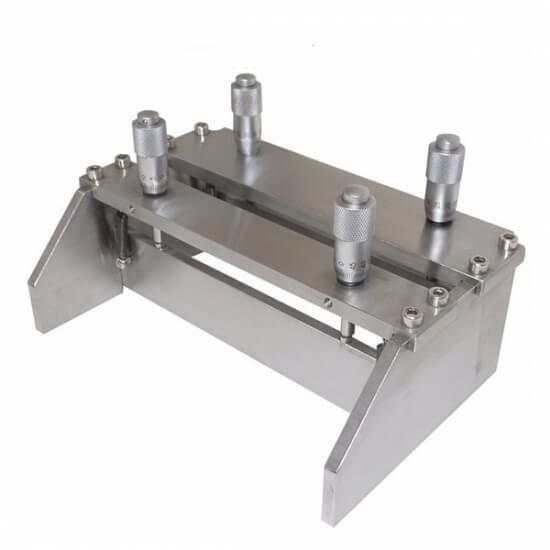