Lith Corporation, founded in 1998 by a group of material science doctor from Tsinghua University, has now become the leading manufacturer of battery lab&production equipment. Lith Corporation have production factories in shenzhen and xiamen of China.This allows for the possibility of providing high quality and low-cost precision machines for lab&production equipment,including: roller press, film coater,mixer, high-temperature furnace, glove box,and complete set of equipment for research of rechargeable battery materials. Simple to operate, low cost and commitment to our customers is our priority.
What is a Prismatic Cell Pack Line?
A Prismatic Cell Pack Line refers to the complete set of machinery, systems, and processes used to assemble prismatic lithiumion battery cells into modules, and then integrate those modules into full battery packs. These lines are essential for manufacturing highperformance battery systems used in electric vehicles (EVs), energy storage systems (ESS), and industrial applications such as forklifts, AGVs (autonomous guided vehicles), and mining equipment.
Prismatic cells are rigid, rectangularshaped batteries typically housed in aluminum or steel casings. Compared to cylindrical or pouchtype cells, they offer better structural stability and are easier to stack and integrate into modular designs — making them ideal for packlevel assembly.
Key Stages of a Prismatic Cell Pack Line
The production process on a prismatic cell pack line consists of several carefully coordinated stages to ensure the final battery pack meets performance, safety, and reliability standards.
1. Cell Inspection and Sorting
Incoming prismatic cells are tested for voltage, internal resistance, and capacity.
Cells are sorted based on performance characteristics to ensure consistency across modules.
Ensures balanced performance and longevity of the final pack.
2. Module Assembly
Qualified cells are stacked and arranged into module configurations.
This stage may involve:
Manual fixtures
Semiautomatic systems
Fully automated robotic assembly lines
Insulation materials, cooling plates, and sensors are added during this phase.
3. Busbar Welding
Electrical connections between cells are made by welding metal busbars (typically copper or aluminum).
Common techniques include:
Laser welding
Ultrasonic welding
Precision is critical to ensure low electrical resistance and mechanical durability.
4. Housing Installation
Modules are placed into protective housings.
Additional components such as thermal interface materials (TIM), fasteners, and connectors are installed.
Some designs incorporate liquid cooling channels at this stage.
5. Leak and Pressure Testing
If the design includes liquid cooling, modules undergo pressure or leak testing.
Ensures there are no coolant leaks that could lead to performance issues or safety hazards.
6. Electrical and Functional Testing of Modules
Each module is tested for:
Voltage balance
Insulation resistance
Communication with the Battery Management System (BMS)
Data from these tests is often stored digitally for traceability.
7. Battery Pack Integration
Multiple modules are mounted inside the final battery pack enclosure.
The Battery Management System (BMS) is integrated along with wiring harnesses, cooling systems, and control electronics.
This step may also involve mounting brackets, covers, and safety interlocks.
8. Final Pack Testing
The completed battery pack undergoes comprehensive functional testing:
Full charge/discharge cycles
Thermal performance validation
Communication checks with vehicle or system controllers
Ensures the pack meets all required performance and safety standards.
9. Packaging and Dispatch
After passing all quality checks, the battery pack is labeled, documented, and prepared for shipment.
Packaging includes foam inserts or custom crates to protect the unit during transport.
Automation Levels in a Prismatic Cell Pack Line
Depending on the production goals, budget, and scale, automation levels can vary significantly:
Manual Operations: Suitable for smallscale production, prototyping, or R&D environments where human involvement is high.
SemiAutomatic Systems: Combine automated functions (e.g., welding, testing) with manual handling for flexibility and cost efficiency.
Fully Automated Lines: Highspeed, robotdriven setups used in largescale EV or ESS production facilities. These lines often include AIbased vision systems, realtime data tracking, and MES integration.
Pouch Cell Fabrication
Design Considerations for Building a Prismatic Cell Pack Line
When planning a new prismatic cell pack line, several key factors must be considered:
Cell Compatibility: Ensure the line supports your specific prismatic cell dimensions and format.
Production Volume: Determine daily output requirements to select appropriate equipment and layout.
Factory Layout and Workflow: Optimize the flow of materials and workstations to minimize bottlenecks and maximize throughput.
Thermal Management Requirements: Whether the system uses aircooling or liquidcooling affects module and pack design.
Integration with BMS: Seamless communication between the battery modules and the BMS is essential for safe and efficient operation.
Safety Features: Include fire suppression systems, emergency stop mechanisms, and explosionproof enclosures where necessary.
Traceability and Digital Integration: Implement Manufacturing Execution Systems (MES) for full traceability and datadriven quality control.
Applications of Prismatic Cell Pack Lines
These lines produce battery systems for a wide range of sectors, including:
Electric Vehicles (EVs): Passenger cars, buses, commercial trucks, delivery vans
Energy Storage Systems (ESS): Gridscale storage, renewable energy integration, peak shaving, and backup power
Industrial Equipment: Electric forklifts, autonomous guided vehicles (AGVs), mining machines
Transportation: Electric trains, ships, boats, and marine vessels
Benefits of Operating a Prismatic Cell Pack Line
Enables scalable and repeatable production of highquality battery systems
Offers excellent mechanical stability and thermal management capabilities
Supports both smallbatch and massvolume production
Reduces failure risks compared to pouchtype cells
Facilitates advanced automation and digital monitoring
Improves product consistency and reduces labor costs through automation
Leading Companies Providing Solutions for Prismatic Cell Pack Lines
Several global companies specialize in providing turnkey solutions or key components for prismatic cell pack lines:
KUKA Systems – Advanced robotic automation for battery assembly
B&R Industrial Automation (ABB) – Integrated automation platforms
Gree EnergyTech – Complete battery module and pack line solutions
Hanson Robotics – Smart battery manufacturing systems
Hyundai WIA – Specialized equipment for automotive battery production
EnerSys – Experts in energy storage system integration
Tesla (inhouse developed systems) – Custombuilt lines for Gigafactories
Need Help Planning Your Prismatic Cell Pack Line?
If you're looking to design, build, or optimize your prismatic cell pack line, I can help you with:
Process flow and production planning
Factory layout and space optimization
Equipment selection and automation strategy
Supplier recommendations and cost estimation
Customization based on your specific application and production goals
All you need to do is provide the following information:
Cell dimensions and chemistry
Desired production volume per day
Level of automation needed (manual/semiauto/fullauto)
Target application (EV, ESS, industrial, etc.)
With this data, I can help you create a tailored, efficient, and futureready prismatic cell pack line solution.
Let me know how I can assist you further!
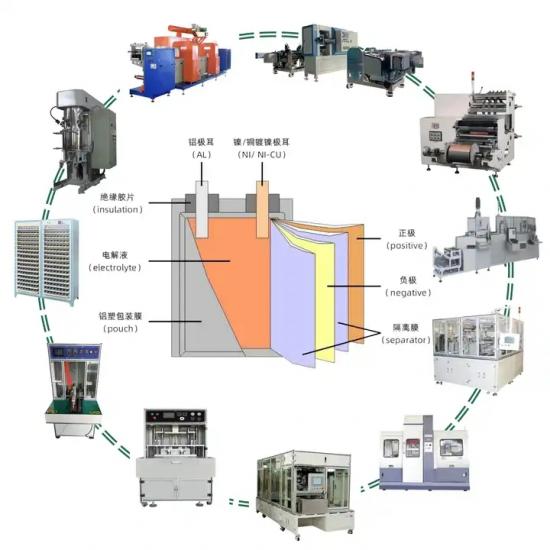