Lith Corporation, founded in 1998 by a group of material science doctor from Tsinghua University, has now become the leading manufacturer of battery lab&production equipment. Lith Corporation have production factories in shenzhen and xiamen of China.This allows for the possibility of providing high quality and low-cost precision machines for lab&production equipment,including: roller press, film coater,mixer, high-temperature furnace, glove box,and complete set of equipment for research of rechargeable battery materials. Simple to operate, low cost and commitment to our customers is our priority.
An Electrode Coater is specialized equipment used primarily in the manufacturing of batteries, particularly for coating electrodes used in lithiumion and other types of rechargeable batteries. The process involves applying a slurry (a mixture of active material, binders, and conductive additives) onto metal foils (typically copper for anodes and aluminum for cathodes). This coated foil forms the electrode, which is a critical component in the battery's performance and efficiency.
Key Features
1. Precision Application
Electrode coaters are designed to apply the slurry with high precision, ensuring uniform thickness across the entire width of the foil. This uniformity is crucial for maintaining consistent battery performance.
2. Coating Methods
Common methods include slot die coating, comma coating, and reverse roll coating. Each method has its advantages depending on the specific requirements of viscosity, drying time, and desired coating thickness.
3. Drying Systems
After the slurry is applied, it must be dried to remove solvents and solidify the coating. Efficient drying systems, such as hot air dryers, infrared heaters, or UV curing units, are integral parts of the electrode coating process.
4. Automation and Control
Modern electrode coaters feature advanced automation capabilities that allow for realtime monitoring and adjustment of key parameters like coating speed, tension control, and temperature. These features help maintain quality and consistency throughout the production process.
5. Flexibility and Versatility
Designed to handle various types of slurries and substrates, these machines can be adapted for different battery chemistries and configurations, making them highly versatile for research and development as well as production environments.
6. Safety Measures
Given the nature of the materials involved, especially solvents used in the slurry, safety measures such as ventilation systems, explosionproof designs, and emergency stop functions are essential to protect operators and comply with safety regulations.
Battery Slot Die Coater
Applications
Battery Manufacturing: Primarily used for producing electrodes for lithiumion batteries, which are used in portable electronics, electric vehicles, and renewable energy storage systems.
Research and Development: Electrode coaters are also utilized in labs for developing new battery technologies and testing different formulations of active materials, binders, and conductive additives.
Considerations When Choosing an Electrode Coater
Application Requirements: Consider your needs regarding coating thickness, substrate type, and material compatibility to ensure the machine meets your specifications.
Production Scale: Choose a machine that aligns with your production volume, whether you're conducting smallscale R&D trials or largescale industrial production.
Budget Constraints: Balance initial investment costs against longterm operational benefits, taking into account maintenance, energy consumption, and potential productivity gains.
Ease of Use and Maintenance: Opt for userfriendly interfaces and straightforward maintenance procedures to minimize downtime and training.
Scalability and Future Growth: Ensure the machine supports scalability and adaptability to future production demands or technological advancements.
Compliance Standards: Verify that the machine complies with relevant industry standards and regulations, especially important in regulated fields like battery manufacturing.
By carefully evaluating these considerations, you can select an Electrode Coater that not only fits your current production needs but also supports future growth and compliance requirements. Ensuring highquality, consistent coatings is fundamental to the performance of batteries, making the selection of appropriate coating equipment a critical decision for manufacturers in this sector. Manufacturers specializing in coating technology often provide a range of electrode coaters tailored to different applications and scales of production. Consulting directly with these manufacturers can help identify the most suitable model for specific needs. Examples of such manufacturers might include companies known for their expertise in battery manufacturing equipment, such as Hirano Tecseed, DOWA Engineering, and others renowned for providing precise and reliable coating machinery.
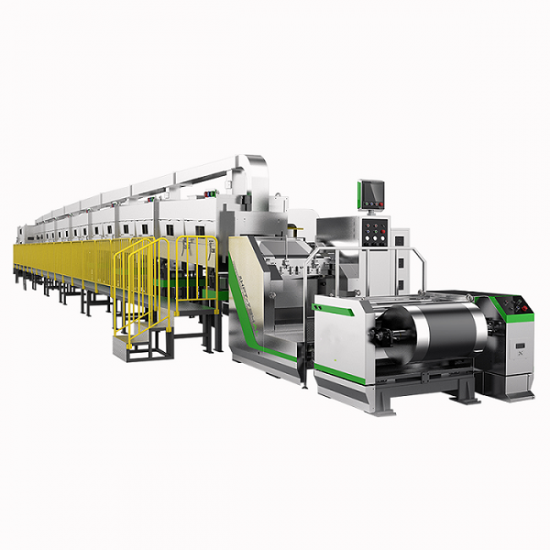