Lith Corporation, founded in 1998 by a group of material science doctor from Tsinghua University, has now become the leading manufacturer of battery lab&production equipment. Lith Corporation have production factories in shenzhen and xiamen of China.This allows for the possibility of providing high quality and low-cost precision machines for lab&production equipment,including: roller press, film coater,mixer, high-temperature furnace, glove box,and complete set of equipment for research of rechargeable battery materials. Simple to operate, low cost and commitment to our customers is our priority.
A film casting machine, also known as a film extrusion or cast film machine, is specialized equipment designed to produce thin, uniform films from various thermoplastic materials. This process involves melting the raw material (usually in pellet form), then extruding it through a flat die to form a continuous film that is subsequently cooled and solidified on a chilled roller. Film casting machines are widely used across industries such as packaging, agriculture, construction, and manufacturing for producing products like food packaging films, shrink wrap, agricultural films, and more.
Key Features
1. Extrusion Unit
The heart of a film casting machine is its extruder, which heats and melts the polymer pellets. The screw design within the extruder plays a critical role in ensuring proper mixing and flow of the molten material.
2. Die Design
The flat die through which the molten polymer is extruded is designed to ensure even distribution of the material, leading to a uniform film thickness. Advanced designs may include automatic lip adjustments for varying thicknesses.
3. Cooling System
After exiting the die, the molten film passes over one or more chill rolls (typically watercooled) to rapidly cool and solidify it. The temperature and speed of these rolls are crucial for achieving desired film properties.
4. Film Thickness Control
Modern film casting machines incorporate precise controls to manage film thickness across the width, often using feedback loops with sensors to make realtime adjustments.
5. Winding System
Once cooled and solidified, the film is wound onto rolls. Highprecision winding systems ensure the film is rolled tightly and evenly, minimizing defects like wrinkles or air pockets.
6. Automation and Control Systems
These machines are equipped with advanced automation features that enhance efficiency, reduce waste, and improve product quality. They allow for monitoring and adjusting key parameters like temperature, pressure, and speed throughout the process.
7. Versatility
Capable of handling a variety of polymers including polyethylene (PE), polypropylene (PP), polyvinyl chloride (PVC), and others. Some machines are configured to handle multilayer films by coextruding different materials simultaneously.
Film Applicator Coater
Applications
Packaging: Produces films for food packaging, shrink wrap, stretch wrap, and other consumer goods packaging.
Agriculture: Used for creating mulch films, greenhouse covers, and silage wraps that help in crop protection and growth enhancement.
Construction: Manufactures vapor barriers, protective sheeting, and geomembranes for waterproofing and soil stabilization.
Medical: Creates sterile packaging films and medical drapes that require high standards of cleanliness and consistency.
Considerations When Choosing a Film Casting Machine
Material Compatibility: Ensure the machine can handle the specific polymers you intend to use, considering factors like viscosity and processing temperatures.
Production Volume: Select a machine that matches your production needs, whether you're focusing on smallscale custom runs or largescale industrial output.
Film Specifications: Look for machines capable of achieving the desired film thickness, width, and surface finish for your applications.
Budget Constraints: Balance initial investment against longterm operational costs, factoring in maintenance, energy consumption, and potential productivity gains.
Ease of Operation and Maintenance: Opt for userfriendly interfaces and straightforward maintenance procedures to minimize downtime and training requirements.
Compliance Standards: Verify that the machine meets relevant industry standards and regulations, particularly important in regulated fields like food packaging and pharmaceuticals.
By carefully evaluating these considerations, you can select a film casting machine that not only satisfies your current production needs but also supports future growth and compliance requirements. Ensuring highquality, consistent films is fundamental to many manufacturing processes, making the selection of appropriate machinery a critical decision for manufacturers across various sectors. Manufacturers specializing in film extrusion technology often provide a range of film casting machines tailored to different applications and scales of production. Consulting directly with these manufacturers can help identify the most suitable model for specific needs. Examples of such manufacturers might include companies known for their expertise in this field, such as DavisStandard, Windmöller & Hölscher, and others renowned for providing robust and reliable film casting solutions.
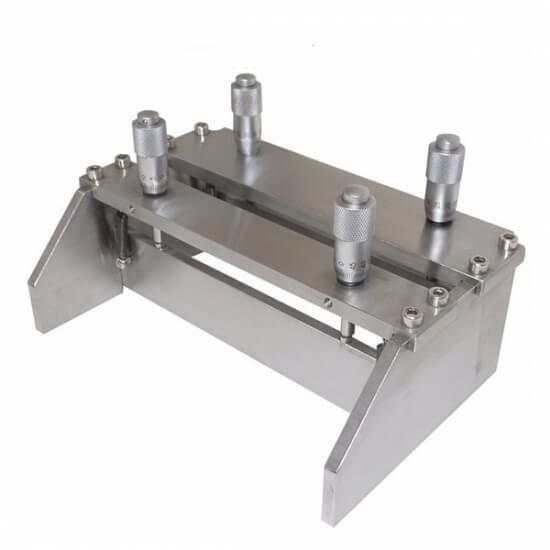