Lith Corporation, founded in 1998 by a group of material science doctor from Tsinghua University, has now become the leading manufacturer of battery lab&production equipment. Lith Corporation have production factories in shenzhen and xiamen of China.This allows for the possibility of providing high quality and low-cost precision machines for lab&production equipment,including: roller press, film coater,mixer, high-temperature furnace, glove box,and complete set of equipment for research of rechargeable battery materials. Simple to operate, low cost and commitment to our customers is our priority.
A Forced Internal-Short Circuit Tester is specialized equipment designed to evaluate the safety and stability of batteries by intentionally creating internal short circuits. This type of testing is crucial for understanding how a battery behaves under conditions that could lead to thermal runaway, a chain reaction within the battery leading to overheating, fire, or explosion. Such tests are vital for ensuring the safety and reliability of lithium-ion and other types of batteries used in consumer electronics, electric vehicles (EVs), and energy storage systems.
Key Features
1. Internal Short Circuit Induction
The tester uses a method, such as the nail penetration test or an induced defect approach, to create a controlled internal short circuit within the battery cell. This helps simulate scenarios where physical damage or manufacturing defects might cause internal shorts.
2. Precision Control
Offers precise control over the parameters of the short circuit induction process, including the position, speed, and force applied during the creation of the short circuit. This precision is essential for replicating specific failure modes and assessing their impact on battery safety.
3. Safety Features
Given the potential hazards associated with inducing internal shorts in batteries, these testers are equipped with robust safety features. These may include protective enclosures, automatic shutdown mechanisms upon detection of unsafe conditions, exhaust systems for fume extraction, and sometimes remote operation capabilities.
4. Data Acquisition System
Advanced testers come with integrated data acquisition systems to monitor and record key parameters during the test, such as voltage, temperature, pressure changes, and any emissions. This data is critical for analyzing the behavior of the battery during and after the induced short circuit.
5. Customizable Test Protocols
Users can customize test protocols based on specific standards or requirements. For example, standards like UL 9540A focus on evaluating thermal runaway fire propagation in battery energy storage systems, while others like SAE J2464 provide guidelines for conducting abuse tests on EV battery packs.
6. Environmental Controls (Optional)
Some high-end models may offer environmental chambers to conduct tests under controlled temperature and humidity conditions, simulating extreme environments where the battery might be used or stored.
Battery Short Circuit Tester
Applications
Consumer Electronics: Ensuring that batteries in devices like smartphones, laptops, and wearables can safely handle internal short circuit conditions.
Electric Vehicles (EVs): Critical for assessing the safety of EV battery packs against internal short circuits that could lead to thermal runaway.
Energy Storage Systems: Verifying the robustness of large-scale battery systems used in renewable energy installations against internal short circuit failures.
Regulatory Compliance: Helps manufacturers comply with international safety standards and regulations governing battery safety, such as UN/DOT 38.3, IEC 62133, UL 1642, and others.
Considerations When Choosing a Forced Internal-Short Circuit Tester
Test Requirements: Ensure the tester meets your specific test protocols, including the method of short circuit induction, parameter controls, and required data recording capabilities.
Battery Size and Type: Select a tester capable of accommodating the size and chemistry of batteries you intend to test.
Budget Constraints: Costs vary based on capacity, features, and brand. Determine which features are necessary versus those that are optional.
Ease of Use: Look for user-friendly interfaces and straightforward maintenance procedures to minimize downtime and training requirements.
Maintenance and Support: Consider the availability of spare parts, customer support, and maintenance services offered by the manufacturer.
Compliance Standards: Verify that the tester complies with relevant industry standards and certifications required for your application, such as UL, IEC, or UN standards.
By carefully considering these factors, you can select a Forced Internal-Short Circuit Tester that not only fits your current testing needs but also supports future growth and compliance requirements. Ensuring the safety and reliability of batteries through rigorous internal short circuit testing is essential for enhancing product safety across numerous industries.
Manufacturers specializing in battery testing solutions often provide Forced Internal-Short Circuit Testers as part of their offerings. It's advisable to consult directly with these manufacturers or suppliers to find a solution tailored to your specific requirements and ensure it meets all necessary safety and performance standards. Examples of such manufacturers could include companies known for their comprehensive range of material and product testing equipment, such as Arbin Instruments, Maccor, and others.
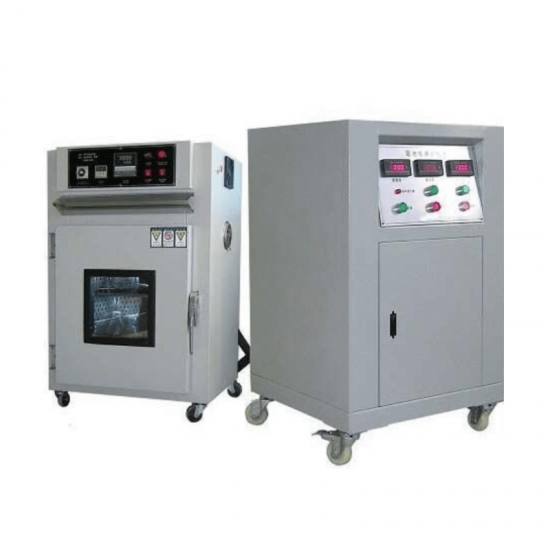